Not a Chip off the Old Block
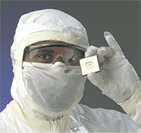
Texas Instruments is constructing an innovative new million-square-foot microchip fabrication plant in Texas, thanks to a little help from the落基山研究所。克里斯蒂娜页
Paul Westbrook would love to show you his house. It's a passive-solar, award-winning structure in Fairview, Texas that uses a third of the electricity and less than a fourth of the water of conventional homes in the region. It's got superwindows, an aerobic septic treatment system, active solar water heating, a geothermal heat-pump heating system, and a pair of 1,600-gallon rainwater tanks. Its design details, favorable economics, and carefully measured performance are all postedonline。
实现资源利用效率和共享有关它的信息是两个威斯布鲁克的天赋。当他不向人们展示节能设计,系统,并在他的家庭设备,他的努力,使这些创新给他的公司 - 德州仪器,在那里他是可持续发展的设计经理。
当布鲁克遇到关于从占用能量的阴极射线管的计算机屏幕切换到平面显示器的成本效益的怀疑,他写表示从能源等积蓄全公司的利益的广泛的电子表格。但他心中有更高的目标。当落基山研究所CEO埃默里·洛文斯在2001年解决可持续发展的达拉斯事件,威斯布鲁克抢到他给在TI的研讨会上有效的“晶圆厂” - 芯片制造工厂。2003年春,艾默里回到TI;人群要大得多和兴趣日益浓厚。约可持续性和整体系统设计的机会提高认识,威斯布鲁克带来立体TI副总裁到他家,向他们展示了他的水必威体育2018电费(就像RMI已经在其超高效的总部完成)。这引起了他们的注意 - 并且让他们谈对公司的影响。“这有助于证明,运用良好的设计可以允许以最少的资金投入一个更高效的系统,”威斯布鲁克指出。
A year and a half later, on 18 November 2004 in Richardson, Texas, TI broke ground on a state-of-the-art, high-efficiency, million-square-foot chip fab (including 220,000 square feet of clean room), designed in part with ideas generated during a three-day charrette1 with Rocky Mountain Institute.
RMI has worked for chipmakers before -- mainly consulting for another world leader,STMicroelectronics。During 1998–2000, RMI's experts surveyed eight ST fabs, finding large potential savings with fast paybacks. Sure enough, STMicroelectronics (like IBM and DuPont) has been cutting its energy use per unit of production by 6% every year, paying back in 2–3 years. But at TI, RMI had the prized opportunity to help design a new chip fab from scratch -- bound to save more and cost less than retrofitting old ones. Normally, in the boom-and-bust chip business, redesigning the next fab is either premature or too late; there's never a good time to do it. But Westbrook astutely timed his intervention, and engaged RMI just in time to change the design mentality, both in his firm and in its equipment providers and consulting engineers.
当德州仪器官员首次开始讨论他们的新工厂,可持续发展是不是在他们的头脑中最重要的事情。必威体育2018晶圆厂是复杂的,极为资本密集(往往数十亿美元),以及高耗能的。亚微观的众多芯片层,具有功能比流感病毒更小,蚀刻,溅射,和异国情调的高科技“工具”出炉到硅晶片上的气候控制里面的“洁净室”。芯片制造是破坏和污染极其敏感。可靠性是至关重要的 - 生产中断可能花费超过100万,每天$。工人必须保持舒适的内部特殊的工作服,以防止灰尘和绒毛出来的超洁净的(最小的斑点可能毁掉一个芯片,其特点是不到十万分之一跨越英寸)。该工具的需要精确控制温度和湿度可以更加关键。
在成本竞争,德克萨斯州Instruments was seriously considering building its new facility overseas. But of course fab's high cost is due not just to its specialized tools but also to the scale and complexity of the elaborate equipment that provides abundant chilled water, clean air, scrubbed exhaust, vacuum, and other "utilities." Using those services more frugally can make the fab cost less, work better, build faster, and win in the marketplace. -- -- In 2003, Chris Lotspeich, who'd led much of RMI's ST work, nicely summarized the challenges of chip fabs: --
Now came the hard part: TI's engineers and designers were told to cut the building and utilities cost by 30% over the previous project. "The cost challenge could have been a show-stopper," Westbrook said, "but turned out to be a benefit. We literally had to go back to the drawing board on many items. It gave us a chance to analyze old assumptions and challenge some conventional wisdom. RMI CEO Amory Lovins calls it 'good old Victorian engineering'" -- the art of wringing multiple benefits from single expenditures.
开车的革命性的变化和抛弃cremental evolutionary design, the 30-percent-lower-capital-cost goal gave Westbrook and his unfunded "Fabscape" sustainability design team their opening to test the most innovative ideas. Starting in 2002, the team met every two weeks and generated a flurry of state-of-the-art concepts.
Their growing stack of white papers soon made a compelling case for a freewheeling-but-disciplined design process to distill out something useable. So in December 2003, a team of RMI consultants came to help TI bubble up and boil down hundreds of nifty notions into twelve "Big Honkin' Ideas" -- concepts that could fundamentally change how TI designed and built a fab and how TI worked with its industrial partners.
A wafer fab is full of exquisitely complex tools made by arcanely specialized suppliers. Energy efficiency is rarely a consideration when specifying tools. Because process and reliability requirements rule, the customer seldom asks for efficiency, and the toolmaker, who won't pay the utility bills, simply isn't used to providing it. It's not that they can't; rather, they've never been asked.
然而,累积效应allthe power consumed byallthe fab's tools and equipment led the charrette participants to trace how each watt of energy consumed by each tool ends up as heat that must be removed, making the cooling equipment bigger and power-hungry -- at a total present-valued cost around $7 per watt! So the biggest win wouldn't be simply making the cooling equipment more efficient, but making it smaller and simpler by buying efficient tools that would give off less heat in the first place. Equipment would be sized by measurement, not guesswork: as RMI designers say (borrowing from GM), "In God we trust; all others bring data."
储蓄迅速开始滋生和繁殖。近一倍效率真空泵,切到怠速等待晶片时,保存的300吨冷却器的容量和工厂的总发电量的7%。真空泵供应商,最初由额外的效率要求一震,很快就看到了业务逻辑。优化的温度和压力下降保存的内部冷却的工具的冷却水流量的五分之一。每个价值为$ 62现值 - 聪明排气系统排气和它的置换(调节的新鲜空气)的保存100000立方英尺每分钟(cfm)。内部冷却与旨在少输压力和温度级联成一个3000加仑每分钟减少在中央处理冷却水系统的尺寸热交换器工具,既节省了资本和操作成本。
As post-workshop design progressed, it became increasingly apparent that smarter tools and their smaller, more efficient supporting systems would cascade energy and water savings. The results included a split chiller plant that cools water to two different temperatures for different purposes (further innovation might even eliminate one of the two sections in the next fab); highly efficient fan filter units for air recirculation; prechilling incoming hot air with outgoing cool air; big pipes and small pumps to cut friction and capital cost; natural daylighting and highly efficient lighting fixtures in the office area; solar water heating; a reflective roof; and extensive water recycling and reuse (reclamation will save nearly a million gallons of city water per day). Recovering heat previously thrown away, and using high-pressure water spray rather than steam for humidification, reduced six boilers to just one plus a backup -- both of which will be off most of the year -- cutting emissions of nitrogen oxides by 60%.
Although the facility will have to be up and running before anyone can know for sure, Westbrook predicts that the new facility will cut energy use by 20% and water use by 35% compared with TI's previous wafer fab. The savings come about half each from better tools and their direct support equipment and from smaller, more frugal utilities and building systems.
"Whole-systems tool design" wasn't the only breakthrough idea that emerged from the workshop. For example, TI decided to test lighter-weight smocks for clean room workers. Particle tests revealed that eliminating facemasks shouldn't harm product quality, and could make workers more comfortable with less chilling.
Some of the design features explored at the workshop were standard components of green design for non-industrial buildings, and offered tremendous financial benefit. Each waterless urinal, for example, will save 40,000 gallons of water a year, plus the capital cost of flush valves and water pipes not installed -- helpful to a water-intensive industry in an arid climate. Energy modeling software such as eQUEST3 let the designers test immediately how their ideas would change performance: for example, rotating the administration building 30° could save about $30,000 annually in space cooling.
参与者的多样化的热情迅速集中在赢得了很高的LEED(领先能源与环境设计)的评价 - 以系统的方式,与RMI的帮助下发展而来的,得分为优秀的设计元素。随着威斯布鲁克指出:“人的竞争本质是一种强大的力量,可以被利用好我们想节约能源,减少排放量 - 我们喜欢它,当我们比分这样做的一点。”
The LEED focus seems to be working well for TI. The company will invest $2–3 million in LEED-related items -- mostly efficiency gains that would have been incorporated anyway. That investment will return an estimated $750,000 in operating cost just in the first year, and at full buildout, should save more than $3 million every year.
It'll be exciting to see what comes from those three days in Texas. So far, RMI's retrofit efforts with ST Microelectronics, wrote Lotspeich, have "identified potential HVAC energy savings of 30%–50%, plus other efficiency opportunities. Collectively these retrofits had payback periods of less than two years." But designing a new fab offers far greater scope for doing it right the first time: low-friction pipes and ducts, controls that run motors at the speed instantaneously required, even free cooling by exploiting cool or dry outside air. Such a system at ST's fab near Milan "costs 80% less to operate than conventional cooling, saving $500,000 annually with a payback of one to three years, depending on the weather."
In the end, such bottom-line benefits led TI to adopt most of the Fabscape team's dozen Big Honkin' Ideas (though some await further testing and analysis). All the energy and water savings changed the net capital cost by roughly zero -- at most 1% extra, but quite possibly a decrease. Total capital cost per square foot, as required, came in at 30% below normal, blowing away industry norms and keeping the new fab in the United States.
2005年3月15日,由主要芯片制造商pplied Materials, Amory Lovins will describe TI's breakthrough to the China Semicon exposition in Shanghai. His goal: to foster still further design improvements in China, which has smart engineers and abundant pollution, scarce power and water, and an urge to leapfrog the West. Such competition is good for the world, and further opportunities remain to be exploited. Could the next fab be designed even better, to save 50% of its energy? Seventy percent? Eighty percent? Let's find out. As such radical savings emerge from the next generations of tool and system design, they may work even better and cost even less. With dedicated innovators like Paul Westbrook and his remarkable team, we're off to the races -- helping one of the world's fastest-growing and most advanced industries to reduce all forms of waste to zero.
--------
Christina Page is a researcher/consultant with落基山研究所。
This article has been reprinted courtesy of RMI. It was first printed in the Spring 2005 edition of theRMI Solutions通讯。
Paul Westbrook would love to show you his house. It's a passive-solar, award-winning structure in Fairview, Texas that uses a third of the electricity and less than a fourth of the water of conventional homes in the region. It's got superwindows, an aerobic septic treatment system, active solar water heating, a geothermal heat-pump heating system, and a pair of 1,600-gallon rainwater tanks. Its design details, favorable economics, and carefully measured performance are all postedonline。
实现资源利用效率和共享有关它的信息是两个威斯布鲁克的天赋。当他不向人们展示节能设计,系统,并在他的家庭设备,他的努力,使这些创新给他的公司 - 德州仪器,在那里他是可持续发展的设计经理。
当布鲁克遇到关于从占用能量的阴极射线管的计算机屏幕切换到平面显示器的成本效益的怀疑,他写表示从能源等积蓄全公司的利益的广泛的电子表格。但他心中有更高的目标。当落基山研究所CEO埃默里·洛文斯在2001年解决可持续发展的达拉斯事件,威斯布鲁克抢到他给在TI的研讨会上有效的“晶圆厂” - 芯片制造工厂。2003年春,艾默里回到TI;人群要大得多和兴趣日益浓厚。约可持续性和整体系统设计的机会提高认识,威斯布鲁克带来立体TI副总裁到他家,向他们展示了他的水必威体育2018电费(就像RMI已经在其超高效的总部完成)。这引起了他们的注意 - 并且让他们谈对公司的影响。“这有助于证明,运用良好的设计可以允许以最少的资金投入一个更高效的系统,”威斯布鲁克指出。
A year and a half later, on 18 November 2004 in Richardson, Texas, TI broke ground on a state-of-the-art, high-efficiency, million-square-foot chip fab (including 220,000 square feet of clean room), designed in part with ideas generated during a three-day charrette1 with Rocky Mountain Institute.
RMI has worked for chipmakers before -- mainly consulting for another world leader,STMicroelectronics。During 1998–2000, RMI's experts surveyed eight ST fabs, finding large potential savings with fast paybacks. Sure enough, STMicroelectronics (like IBM and DuPont) has been cutting its energy use per unit of production by 6% every year, paying back in 2–3 years. But at TI, RMI had the prized opportunity to help design a new chip fab from scratch -- bound to save more and cost less than retrofitting old ones. Normally, in the boom-and-bust chip business, redesigning the next fab is either premature or too late; there's never a good time to do it. But Westbrook astutely timed his intervention, and engaged RMI just in time to change the design mentality, both in his firm and in its equipment providers and consulting engineers.
当德州仪器官员首次开始讨论他们的新工厂,可持续发展是不是在他们的头脑中最重要的事情。必威体育2018晶圆厂是复杂的,极为资本密集(往往数十亿美元),以及高耗能的。亚微观的众多芯片层,具有功能比流感病毒更小,蚀刻,溅射,和异国情调的高科技“工具”出炉到硅晶片上的气候控制里面的“洁净室”。芯片制造是破坏和污染极其敏感。可靠性是至关重要的 - 生产中断可能花费超过100万,每天$。工人必须保持舒适的内部特殊的工作服,以防止灰尘和绒毛出来的超洁净的(最小的斑点可能毁掉一个芯片,其特点是不到十万分之一跨越英寸)。该工具的需要精确控制温度和湿度可以更加关键。
在成本竞争,德克萨斯州Instruments was seriously considering building its new facility overseas. But of course fab's high cost is due not just to its specialized tools but also to the scale and complexity of the elaborate equipment that provides abundant chilled water, clean air, scrubbed exhaust, vacuum, and other "utilities." Using those services more frugally can make the fab cost less, work better, build faster, and win in the marketplace. -- -- In 2003, Chris Lotspeich, who'd led much of RMI's ST work, nicely summarized the challenges of chip fabs: --
- Fabs have extensive heating, ventilating, and air conditioning (HVAC) systems with high-performance filters to maintain clean rooms' temperature and humidity precisely while filtering airborne particles. Fans, pumps, furnaces, and chillers deliver conditioned air and cooling water into the clean room via ducts and pipes. Depending on their size, fabs use anywhere from 3 to as much as 30 megawatts of power.2 HVAC systems consume 30%–50% of a fab's electricity; tools use another 40% or so. Energy accounts for [only a few]… percent of a chip's cost, yet electricity can be the largest single [non-labor] operating expense for a chipmaker, totaling millions of dollars annually at a single fab. Moreover, energy-saving measures can improve key operating parameters (yield, setup time, flexibility), and in new plants can save capital and construction time -- critical factors in competitiveness.
- 尽管伟大的创新,半导体制造发展了一个规避风险的企业文化由于在快速变化的市场严格的工艺要求,安全风险,停机成本高,残酷的竞争。会议生产和时间将产品推向市场的目标,需要在成千上万的变量非凡的控制。当一些工作,它是精确复制。公司还建立新的当“复制正是”以前的晶圆厂。这样可以节省一些时间和初始成本,但在该清洁室外延缓改进,其中包括能源效率的特点 - 从而提高经营成本。这有点讽刺的是尖端技术在建筑设计几十年前提出,因此这些建筑现在提供显著节能和省钱的潜力。
Now came the hard part: TI's engineers and designers were told to cut the building and utilities cost by 30% over the previous project. "The cost challenge could have been a show-stopper," Westbrook said, "but turned out to be a benefit. We literally had to go back to the drawing board on many items. It gave us a chance to analyze old assumptions and challenge some conventional wisdom. RMI CEO Amory Lovins calls it 'good old Victorian engineering'" -- the art of wringing multiple benefits from single expenditures.
开车的革命性的变化和抛弃cremental evolutionary design, the 30-percent-lower-capital-cost goal gave Westbrook and his unfunded "Fabscape" sustainability design team their opening to test the most innovative ideas. Starting in 2002, the team met every two weeks and generated a flurry of state-of-the-art concepts.
Their growing stack of white papers soon made a compelling case for a freewheeling-but-disciplined design process to distill out something useable. So in December 2003, a team of RMI consultants came to help TI bubble up and boil down hundreds of nifty notions into twelve "Big Honkin' Ideas" -- concepts that could fundamentally change how TI designed and built a fab and how TI worked with its industrial partners.
A wafer fab is full of exquisitely complex tools made by arcanely specialized suppliers. Energy efficiency is rarely a consideration when specifying tools. Because process and reliability requirements rule, the customer seldom asks for efficiency, and the toolmaker, who won't pay the utility bills, simply isn't used to providing it. It's not that they can't; rather, they've never been asked.
然而,累积效应allthe power consumed byallthe fab's tools and equipment led the charrette participants to trace how each watt of energy consumed by each tool ends up as heat that must be removed, making the cooling equipment bigger and power-hungry -- at a total present-valued cost around $7 per watt! So the biggest win wouldn't be simply making the cooling equipment more efficient, but making it smaller and simpler by buying efficient tools that would give off less heat in the first place. Equipment would be sized by measurement, not guesswork: as RMI designers say (borrowing from GM), "In God we trust; all others bring data."
储蓄迅速开始滋生和繁殖。近一倍效率真空泵,切到怠速等待晶片时,保存的300吨冷却器的容量和工厂的总发电量的7%。真空泵供应商,最初由额外的效率要求一震,很快就看到了业务逻辑。优化的温度和压力下降保存的内部冷却的工具的冷却水流量的五分之一。每个价值为$ 62现值 - 聪明排气系统排气和它的置换(调节的新鲜空气)的保存100000立方英尺每分钟(cfm)。内部冷却与旨在少输压力和温度级联成一个3000加仑每分钟减少在中央处理冷却水系统的尺寸热交换器工具,既节省了资本和操作成本。
As post-workshop design progressed, it became increasingly apparent that smarter tools and their smaller, more efficient supporting systems would cascade energy and water savings. The results included a split chiller plant that cools water to two different temperatures for different purposes (further innovation might even eliminate one of the two sections in the next fab); highly efficient fan filter units for air recirculation; prechilling incoming hot air with outgoing cool air; big pipes and small pumps to cut friction and capital cost; natural daylighting and highly efficient lighting fixtures in the office area; solar water heating; a reflective roof; and extensive water recycling and reuse (reclamation will save nearly a million gallons of city water per day). Recovering heat previously thrown away, and using high-pressure water spray rather than steam for humidification, reduced six boilers to just one plus a backup -- both of which will be off most of the year -- cutting emissions of nitrogen oxides by 60%.
Although the facility will have to be up and running before anyone can know for sure, Westbrook predicts that the new facility will cut energy use by 20% and water use by 35% compared with TI's previous wafer fab. The savings come about half each from better tools and their direct support equipment and from smaller, more frugal utilities and building systems.
"Whole-systems tool design" wasn't the only breakthrough idea that emerged from the workshop. For example, TI decided to test lighter-weight smocks for clean room workers. Particle tests revealed that eliminating facemasks shouldn't harm product quality, and could make workers more comfortable with less chilling.
Some of the design features explored at the workshop were standard components of green design for non-industrial buildings, and offered tremendous financial benefit. Each waterless urinal, for example, will save 40,000 gallons of water a year, plus the capital cost of flush valves and water pipes not installed -- helpful to a water-intensive industry in an arid climate. Energy modeling software such as eQUEST3 let the designers test immediately how their ideas would change performance: for example, rotating the administration building 30° could save about $30,000 annually in space cooling.
参与者的多样化的热情迅速集中在赢得了很高的LEED(领先能源与环境设计)的评价 - 以系统的方式,与RMI的帮助下发展而来的,得分为优秀的设计元素。随着威斯布鲁克指出:“人的竞争本质是一种强大的力量,可以被利用好我们想节约能源,减少排放量 - 我们喜欢它,当我们比分这样做的一点。”
The LEED focus seems to be working well for TI. The company will invest $2–3 million in LEED-related items -- mostly efficiency gains that would have been incorporated anyway. That investment will return an estimated $750,000 in operating cost just in the first year, and at full buildout, should save more than $3 million every year.
It'll be exciting to see what comes from those three days in Texas. So far, RMI's retrofit efforts with ST Microelectronics, wrote Lotspeich, have "identified potential HVAC energy savings of 30%–50%, plus other efficiency opportunities. Collectively these retrofits had payback periods of less than two years." But designing a new fab offers far greater scope for doing it right the first time: low-friction pipes and ducts, controls that run motors at the speed instantaneously required, even free cooling by exploiting cool or dry outside air. Such a system at ST's fab near Milan "costs 80% less to operate than conventional cooling, saving $500,000 annually with a payback of one to three years, depending on the weather."
In the end, such bottom-line benefits led TI to adopt most of the Fabscape team's dozen Big Honkin' Ideas (though some await further testing and analysis). All the energy and water savings changed the net capital cost by roughly zero -- at most 1% extra, but quite possibly a decrease. Total capital cost per square foot, as required, came in at 30% below normal, blowing away industry norms and keeping the new fab in the United States.
2005年3月15日,由主要芯片制造商pplied Materials, Amory Lovins will describe TI's breakthrough to the China Semicon exposition in Shanghai. His goal: to foster still further design improvements in China, which has smart engineers and abundant pollution, scarce power and water, and an urge to leapfrog the West. Such competition is good for the world, and further opportunities remain to be exploited. Could the next fab be designed even better, to save 50% of its energy? Seventy percent? Eighty percent? Let's find out. As such radical savings emerge from the next generations of tool and system design, they may work even better and cost even less. With dedicated innovators like Paul Westbrook and his remarkable team, we're off to the races -- helping one of the world's fastest-growing and most advanced industries to reduce all forms of waste to zero.
--------
Christina Page is a researcher/consultant with落基山研究所。
This article has been reprinted courtesy of RMI. It was first printed in the Spring 2005 edition of theRMI Solutions通讯。